Coup de projecteur sur les cadrans traditionnels
Les amateurs ne le savent pas toujours mais, de tous les composants d’une montre, les cadrans font souvent partie de ceux qui demandent le plus d’opérations manuelles avant montage. Afin de leur offrir de mieux saisir leur importance et de ne pas se tromper dans les termes employés lorsqu’il s’agit de les décrire, voici un petit récapitulatif de ce qu’il faut savoir d’eux.
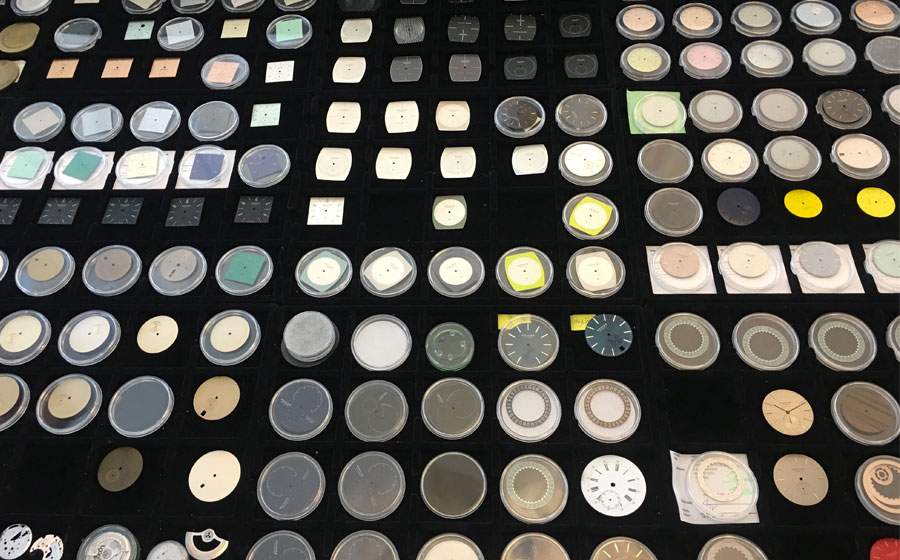
Véritable visage d’un instrument de mesure du temps et reflet des valeurs de son propriétaire, le cadran demande un grand soin lors de sa réalisation car de son équilibre esthétique dépend en grande partie l’appréciation d’une pièce. Au fil des ans, les artistes travaillant avec les horlogers ont mis au point un grand nombre de techniques destinées à augmenter leur valeur perçue. En fonction des périodes et des modes, certaines ont été plus récurrentes que d’autres. Aujourd’hui avec la multiplication des marques et face à l’obligation de se distinguer, les cadrans occupent une place centrale dans la conception de tous les nouveaux produits horlogers.
Email en détail
Les marques les plus attachées à entretenir les métiers d’arts les produisent en émail comme l’étaient la plupart de ceux du passé (après le XVIème siècle). Ces cadrans sont constitués d’un simple disque de métal – en général du laiton ou du cuivre et plus rarement de l’or – sur lequel plusieurs couches d’un minéral vitrifiable à haute température sont passées au four à une température variant de 500° à 800° Celsius. Sur cette base, le plus souvent blanche et opaque, mais pouvant également varier du rouge au noir, sont apposés les chiffres. Ces supports peuvent aussi être peints par des artistes de motifs divers et cuits à chaque opération pour stabiliser les couleurs. Pour donner un rendu brillant et garantir à cet ensemble une inaltérabilité, beaucoup de facteurs recouvrent ces précieux disques en « émail grand feu » d’un fondant transparent appelé dans le métier « une couverte ».
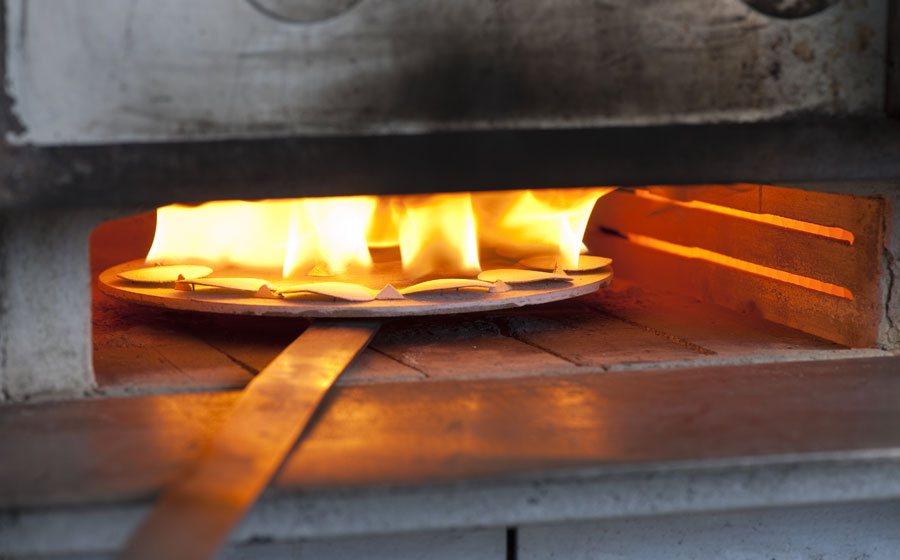
Il existe encore bien d’autres types de cadrans utilisant de l’émail. On pense en premier à ceux qui, portant la dénomination de « flinqués » présentent une surface gravée à la machine, à la main ou même étampée, recouverte d’un émail transparent ou translucide.
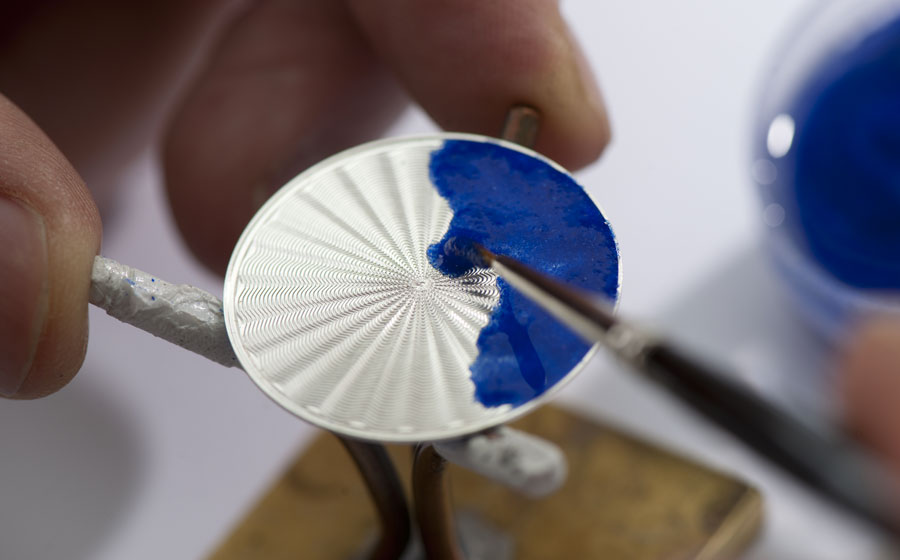
Souvent les professionnels confondent aussi les émaux appelés champlevés et ceux dits cloisonnés. Les premiers sont obtenus à partir d’un disque dans lequel ont été gravés des cavités selon un motif déterminé que les émailleurs remplissent d’une pâte de verre fondue au feu.
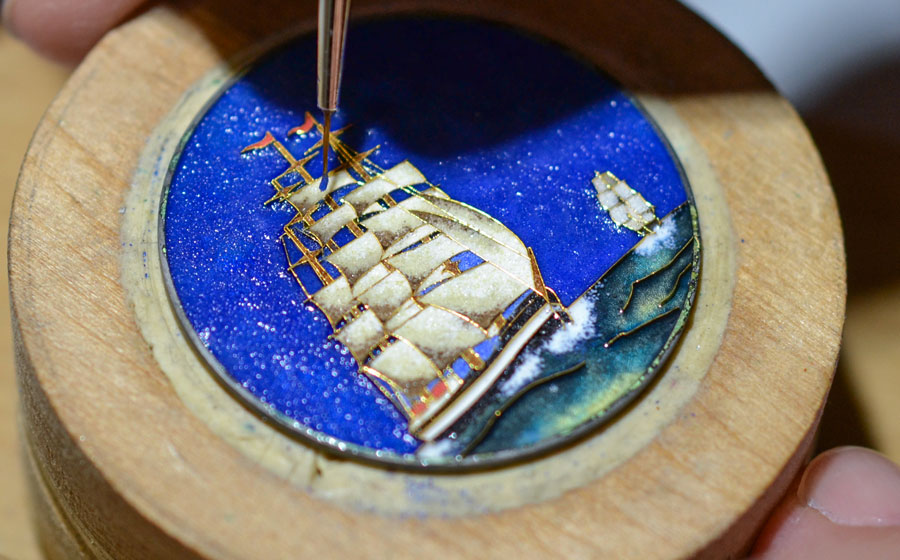
Les seconds sont obtenus par la mise en place sur le disque du cadran de languettes de métal servant à séparer des espaces dans lesquels les artisans émailleurs déposent des cristaux de minéraux vitrifiant à chaud. L’ensemble de ces opérations nécessitant plusieurs cuissons est suivi d’un délicat rodage permettant d’obtenir une surface intégralement plane et polie. Certaines maisons procèdent parfois pour ces cadrans à la pose d’une couverte afin d’augmenter leur brillance.
On notera que le très rare et très fragile cadran en émail « plique-à-jour » est souvent obtenu par la suppression du fond d’un émail cloisonné.
Depuis quelques années, il faut être attentif aux terminologies employées car certaines maisons peu regardantes, se croyant plus malines que les autres, proposent des cadrans « bon marché » réalisés en émail à froid. Autrement dit, obtenus assez facilement et en grande quantité à partir de laques synthétiques polymérisant à l’air.
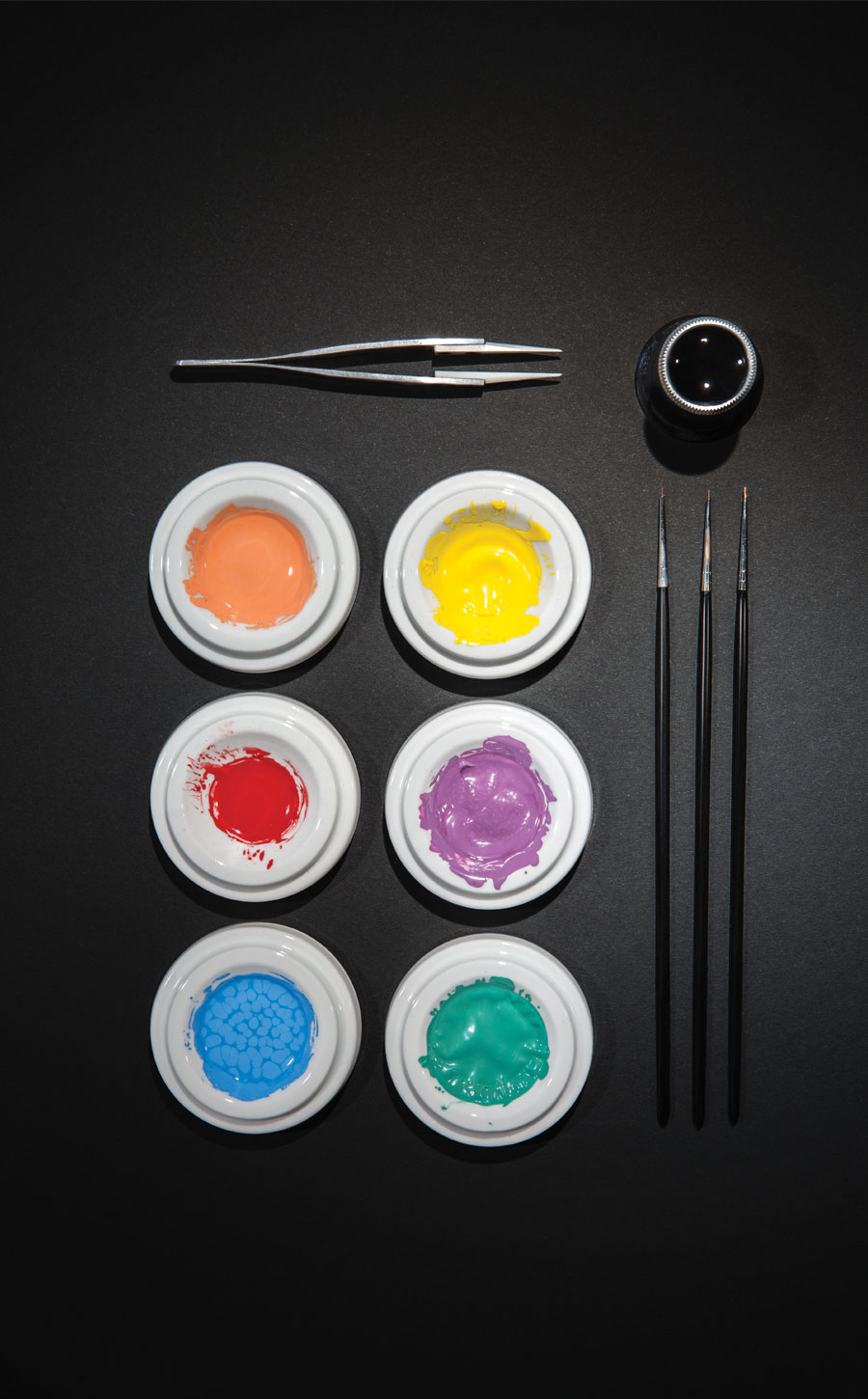
Classiques décors
Certains cadrans présentent une surface couverte de motifs géométriques répétitifs. Dans certains cas rares, ces décors sont réalisés par des artisans, à la main et au burin. A partir du XVIIIème siècle et plus encore au début du XIXème siècle, le guillochage s’est généralisé tant pour les cadrans que pour les boîtiers grâce à la mise au point d’une machine permettant d’exécuter des creusures de façon semi-automatisée. Ces traitements de surface que seules quelques rares marques réalisent encore à l’aide de machines dédiées peuvent aujourd’hui être obtenus bien plus rapidement et pour un coût bien inférieur, par emboutissage, à l’aide de fraiseuses à commandes numériques ou même à partir de lasers spécialisés.
Certains de ces décors sont parfois recouverts d’émail à chaud. Il s’agit de « flinquage ». Quand de très fines gravures obtenues par un traitement de surface circulaire sont peintes ou laquées, on parle dans le métier « d’azurage ».
Le soleillage est obtenu quant à lui par un traitement de surface formé de lignes partant du centre du cadran. Il peut être obtenu en travaillant directement le métal, mais peut être réalisé par un délicat surfaçage du vernis destiné à protéger la peinture ou l’argenture du cadran.
On parle de ramolayé chez les cadraniers (les fabricants de cadrans) lorsque la gravure manuelle ou mécanique est faite en ronde-bosse, le plus souvent dans des matières naturelles comme l’os, l’ivoire ou la nacre.
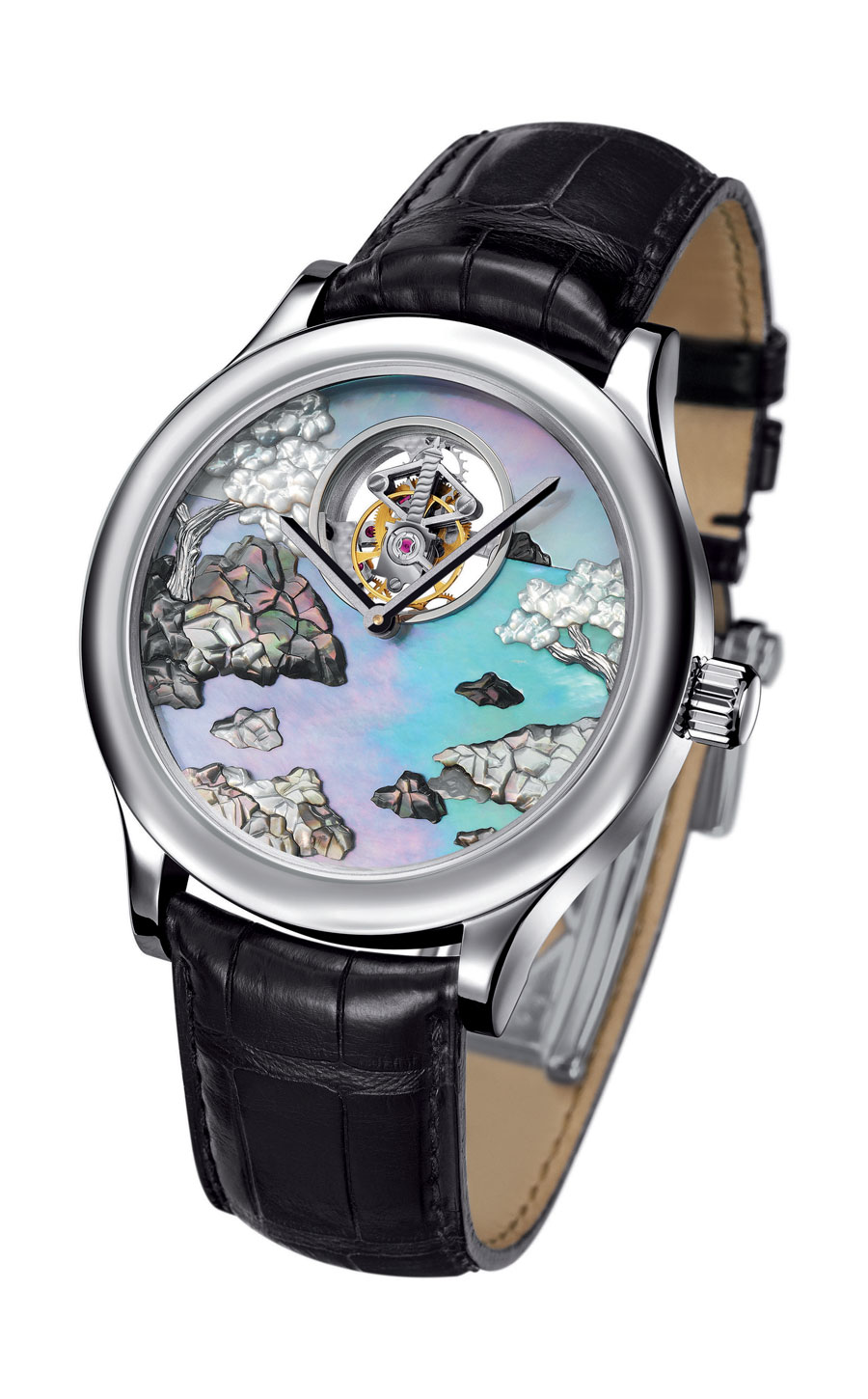
Aujourd’hui, beaucoup de cadrans sont peints ou laqués. Ils sont réalisés par projection au pistolet de peintures fortement chargées en pigments de couleurs ou sur des imprimantes de nouvelle génération. Sur ces bases généralement passées en étuves pour stabiliser les couches de peintures, sont posés différents éléments décoratifs.
D’autres présentent des surfaces argentées, dorées, cuivrées ou rhodiées. Ceux-là sont la plupart du temps réalisés par galvanoplastie, un processus consistant à recouvrir une surface de base avec une couche de métal par électrodéposition. Régulièrement, les marques font appel à la technique PVD, autrement dit un dépôt physique de matière en phase vapeur. On notera que parfois certains cadrans sont réalisés directement en or 18 carats ou en argent 950 rhodié par électrodéposition pour stabiliser ce métal s’oxydant à l’air.
Les logos, les noms de marques, les chemins de fer de minuterie, parfois les chiffres arabes ou romains et les marquages spéciaux sont souvent apposés sur les cadrans par tampographie à l’aide d’un cône en gélatine. Une fois ces opérations effectuées, beaucoup de cadrans reçoivent un vernis de protection cellulosique ou époxydique appelé « Zapon » dans le jargon horloger.
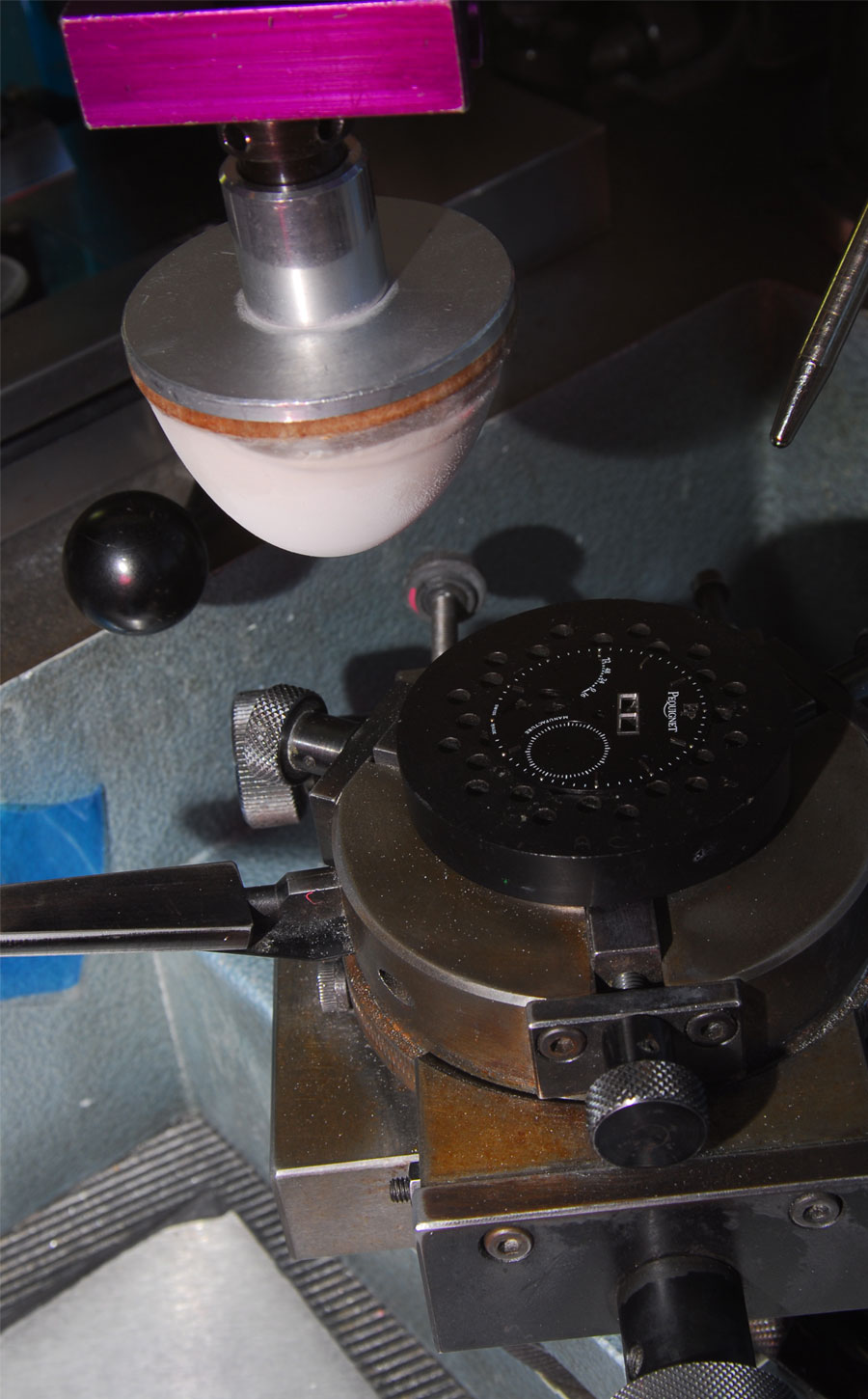
Certains cadrans en cours d’élaboration voient leur surface percée de petits trous. Ils servent à placer les pieds des index métalliques qui peuvent être sertis ou non ou chargés ou pas de matière luminescente non radioactive. Ces petits éléments posés un à un à la main sont ensuite rivés à l’aide d’un outil au dos de la plaque par un ou une opératrice spécialisée. On parle alors de cadran présentant des index en applique.
Parfois, ces appendices en relief ne sont plus rivés, mais simplement collés sur le cadran à l’aide de machines capables de les déposer en une seule opération. Ce traitement appelé « décalque en relief » concerne en général les montres de moyen de gamme, mais il arrive parfois que des modèles à l’orée de la haute horlogerie soient équipés de cadrans réalisés de cette façon.
À lire aussi sur les Métiers d’Art :